NEC、「ケータイができるまで」公開、組み立て・梱包まで流れ作業で約10分
NECは同社の携帯電話を製造する埼玉日本電気(NEC埼玉)をマスコミ向けに公開した。「携帯電話メーカーでは唯一」(九鬼隆訓・NEC埼玉社長)というトヨタ自動車の生産方式「カンバン方式」を取り入れた生産工場で、見学会では効率生産の取り組みをアピールした。
NEC埼玉は84年設立。資本金は2億円でNECが全額出資する。社員は852名。派遣社員や請負作業者を含めた従業員数は2080名。NECの携帯電話の生産拠点として携帯電話と通信基地局を生産。携帯電話ではNTTドコモ向けの端末を製造。薄さ9.8mmの世界最薄端末「N705iμ」や「N905i」などを生産している。
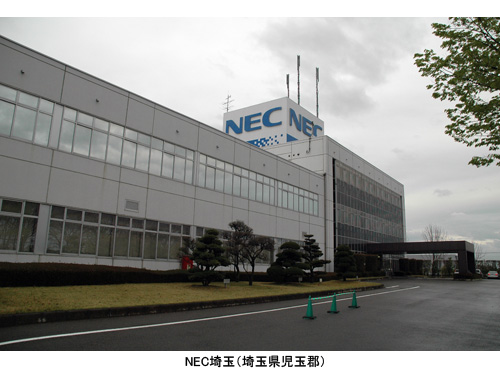
今回報道陣に公開されたのは、部品を基板に実装する「STM(Surface Mount Technology)」、携帯電話の液晶ディスプレイユニットを製造する「LCD工程」、部品保管庫、携帯電話の組み立てを行う「装置トレー」の4か所。
STMは部品をプリント基板に組み込む製造工程。半田印刷と呼ばれる30ミクロンの半田ペーストを基板に印刷。部品を基板に置いた後、250度のリフロー炉(オーブン)に入れて半田を溶かし固定。最後に電気回路の検査と重要部品部分を樹脂で固定する。
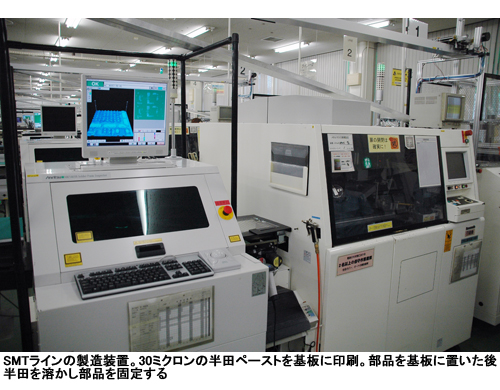
LCD工程は携帯電話の液晶ディスプレイユニットの製造ラインで、ディスプレイ用のガラスをプラズマ洗浄した後、ガラスに駆動用ドライバーやチップを載せ、本体と接続するプリント基板を取り付ける。次に白黒色やカラーの発色、液晶のドット抜けなどの検査を実施。最後にLED(発光ダイオード)のバックライトの組み込みと携帯本体との組み合わせを行う。
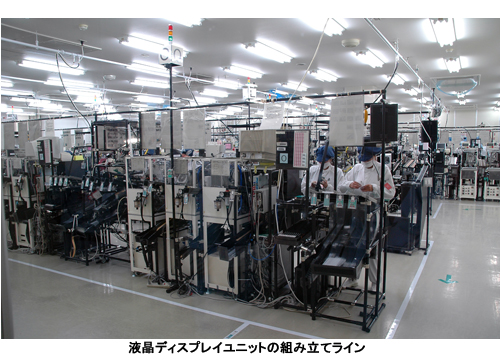
装置トレーではNTTドコモ向けの端末「N905i」の組み立ての様子が公開された。1つのラインは8人の作業員が担当する「グループ型セル生産方式」を導入。「セルにすることで、多品種少量生産や生産機種の変更にも対応できるようした」(今関和雄・NEC埼玉取締役)という。
ラインでは80点の部品をリレー方式で取り付け、最後は機械を使った自動検査までを行う。部品の取り付けから検査後の梱包までの時間は約10分。ラインの長さは11mで、1日に1000台の携帯電話を生産する。
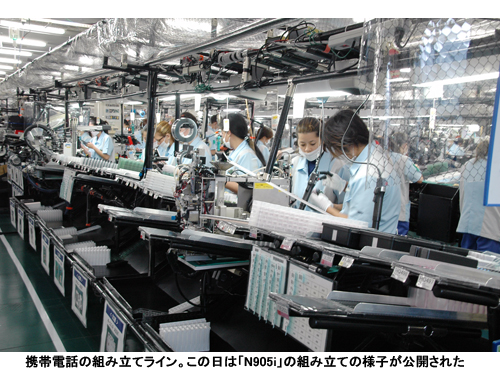
人による取り付けを行っている点について田所武司・NEC埼玉SIP生産革新推進部長は「ケータイのライフサイクルが短いため、機種が変わった場合には人の方がすぐに対応できる。機械では設備投資のコストが高くなる」と説明。加えて「ラインの人同士が助け合ってチームで作業のスピードを確保できる」と話している。
NEC埼玉の生産方式の核はトヨタ自動車が生み出した生産方式「カンバン方式」。部品保管庫「部品ストア」から「水すまし」と呼ぶ部品を各ラインに運ぶ人が保管庫から部品を調達した時に発注書を保管庫に残し、その紙から部品メーカーに不足している部品を発注することで、ムダな在庫の削減し、必要な部品を必要なだけ調達する「ジャスト・イン・タイム」を実現している。
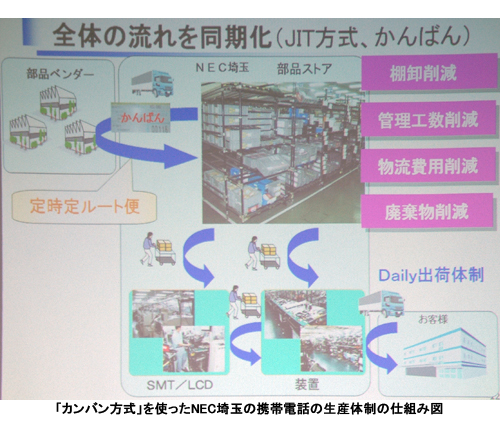
NECでは、トヨタ自動車出身のコンサルタントを招いて、「カンバン方式」を97年頃から導入したという。それまではベルトコンベア方式で生産していたが「カンバン方式」にすることで、物流フロアの面積が3-5分の1に削減。リードタイム(資材などを発注してから納品されるまでの時間)も2-3週間から5日に向上。同時に「品質向上とコスト削減にもつながった
」(九鬼隆訓・NEC埼玉社長)としている。
見学会では、ラインの作業員が作業の流れを体験し、組み立ての習熟度を高めたり、ラインの改善や改良のアイデアを出すための訓練「ものづくり道場」のデモンストレーションも披露された。
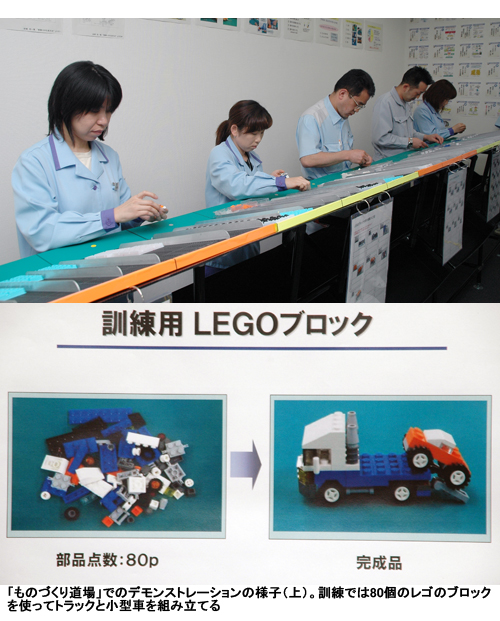
訓練では室内に擬似ラインを設け、レゴ社のブロックを使ってトラックを組み立てる。組み立てに使うブロックの数は80点。今回は5人で1日1000台を作ることを想定したデモが行われた。
今関NEC埼玉取締役は「『ものづくり道場』で作業員が作業スキル向上させるのはもちろん、助け合いを学んでもらったり、ラインの改善案をどんどん出してもらえるようにしていきたい」と抱負を話した。
NEC埼玉は84年設立。資本金は2億円でNECが全額出資する。社員は852名。派遣社員や請負作業者を含めた従業員数は2080名。NECの携帯電話の生産拠点として携帯電話と通信基地局を生産。携帯電話ではNTTドコモ向けの端末を製造。薄さ9.8mmの世界最薄端末「N705iμ」や「N905i」などを生産している。
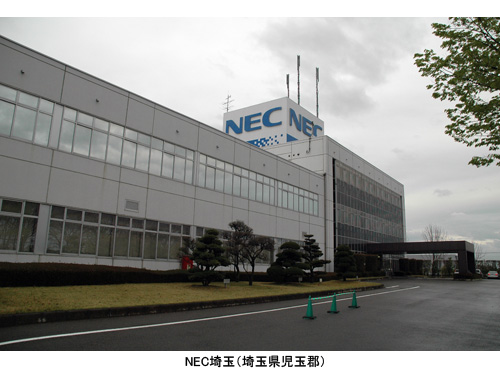
今回報道陣に公開されたのは、部品を基板に実装する「STM(Surface Mount Technology)」、携帯電話の液晶ディスプレイユニットを製造する「LCD工程」、部品保管庫、携帯電話の組み立てを行う「装置トレー」の4か所。
STMは部品をプリント基板に組み込む製造工程。半田印刷と呼ばれる30ミクロンの半田ペーストを基板に印刷。部品を基板に置いた後、250度のリフロー炉(オーブン)に入れて半田を溶かし固定。最後に電気回路の検査と重要部品部分を樹脂で固定する。
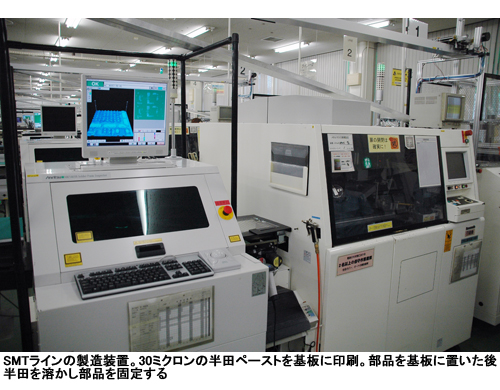
LCD工程は携帯電話の液晶ディスプレイユニットの製造ラインで、ディスプレイ用のガラスをプラズマ洗浄した後、ガラスに駆動用ドライバーやチップを載せ、本体と接続するプリント基板を取り付ける。次に白黒色やカラーの発色、液晶のドット抜けなどの検査を実施。最後にLED(発光ダイオード)のバックライトの組み込みと携帯本体との組み合わせを行う。
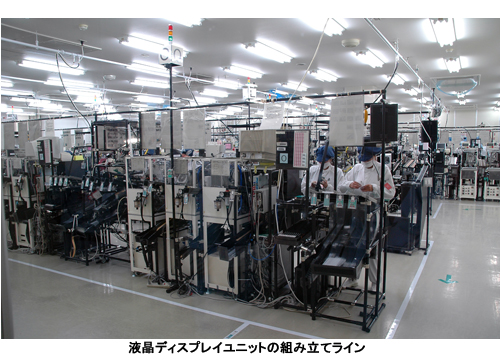
装置トレーではNTTドコモ向けの端末「N905i」の組み立ての様子が公開された。1つのラインは8人の作業員が担当する「グループ型セル生産方式」を導入。「セルにすることで、多品種少量生産や生産機種の変更にも対応できるようした」(今関和雄・NEC埼玉取締役)という。
ラインでは80点の部品をリレー方式で取り付け、最後は機械を使った自動検査までを行う。部品の取り付けから検査後の梱包までの時間は約10分。ラインの長さは11mで、1日に1000台の携帯電話を生産する。
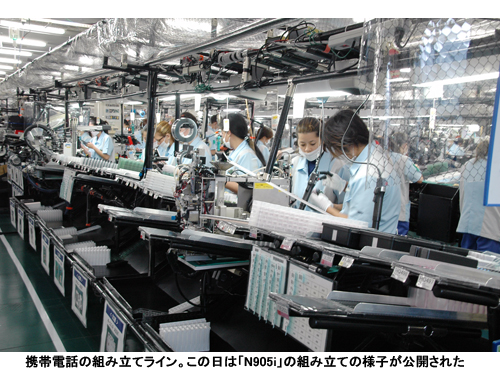
人による取り付けを行っている点について田所武司・NEC埼玉SIP生産革新推進部長は「ケータイのライフサイクルが短いため、機種が変わった場合には人の方がすぐに対応できる。機械では設備投資のコストが高くなる」と説明。加えて「ラインの人同士が助け合ってチームで作業のスピードを確保できる」と話している。
NEC埼玉の生産方式の核はトヨタ自動車が生み出した生産方式「カンバン方式」。部品保管庫「部品ストア」から「水すまし」と呼ぶ部品を各ラインに運ぶ人が保管庫から部品を調達した時に発注書を保管庫に残し、その紙から部品メーカーに不足している部品を発注することで、ムダな在庫の削減し、必要な部品を必要なだけ調達する「ジャスト・イン・タイム」を実現している。
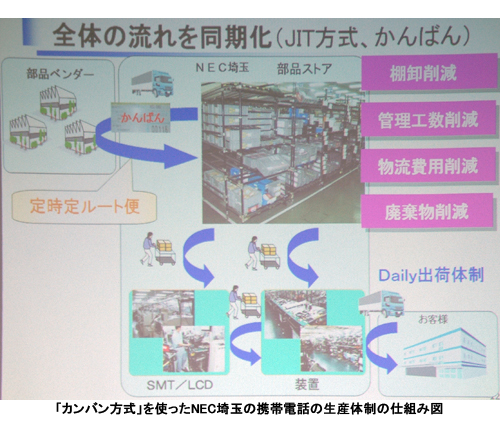
NECでは、トヨタ自動車出身のコンサルタントを招いて、「カンバン方式」を97年頃から導入したという。それまではベルトコンベア方式で生産していたが「カンバン方式」にすることで、物流フロアの面積が3-5分の1に削減。リードタイム(資材などを発注してから納品されるまでの時間)も2-3週間から5日に向上。同時に「品質向上とコスト削減にもつながった
」(九鬼隆訓・NEC埼玉社長)としている。
見学会では、ラインの作業員が作業の流れを体験し、組み立ての習熟度を高めたり、ラインの改善や改良のアイデアを出すための訓練「ものづくり道場」のデモンストレーションも披露された。
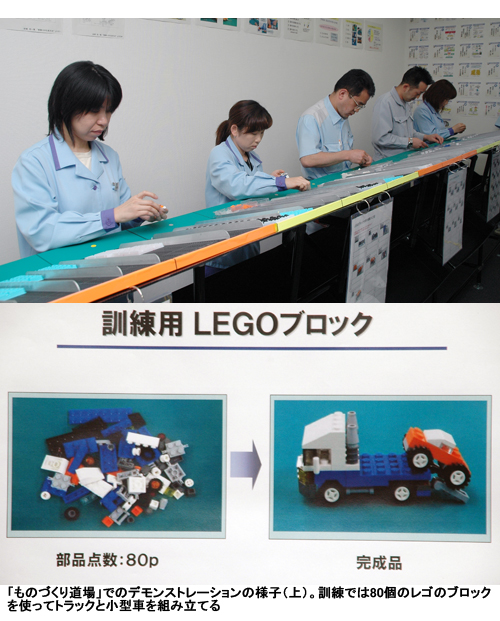
訓練では室内に擬似ラインを設け、レゴ社のブロックを使ってトラックを組み立てる。組み立てに使うブロックの数は80点。今回は5人で1日1000台を作ることを想定したデモが行われた。
今関NEC埼玉取締役は「『ものづくり道場』で作業員が作業スキル向上させるのはもちろん、助け合いを学んでもらったり、ラインの改善案をどんどん出してもらえるようにしていきたい」と抱負を話した。